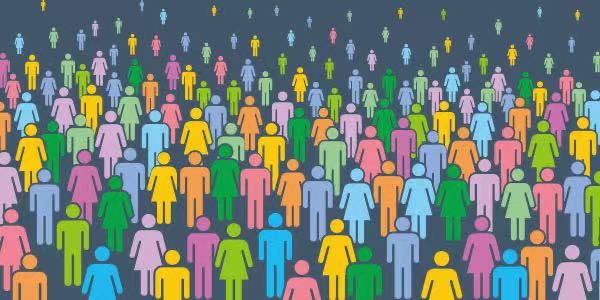
针对我国制造企业日趋严重的劳动力短缺问题,作者提出了两种颇具创新且有针对性的解决方案。
今年2月份人力资源和社会保障部发布的最新“最缺工”榜单显示,自2019年榜单发布以来,制造业类职业在榜单中的占比一直较高,制造业缺工状况持续,智能制造领域缺工程度还在加大,如“多工序数控机床操作调整工”“工业机器人系统操作员”等职业排位处于上升态势。早在2017年发布的《制造业人才发展规划指南》也显示,到2025年,我国制造业10大重点领域人才缺口预计将接近3,000万人,缺口率超过48%。可见,制造业面临着日趋严重的劳动力短缺问题。
“用工荒”困扰制造企业
一般而言,在制造企业员工组成中,20%为管理和技术人员、80%为工厂工人,后者大多为农民工。而国家统计局2021年发布的数据显示,2020年,农民工数量较2019年减少了517万人,其中外出务工人员减少了466万人。另外,近几年来服务业快速发展,新兴行业带来大量新兴职业和岗位,如快递员、外卖员、网约车司机、网络主播等,也极大地分流了制造业劳动力供给。
这些数据显示,曾让我国制造业腾飞的人口红利已然不在,制造企业除了面临原材料价格上涨、供应链延误等不利因素,还将长期受到“用工荒”的困扰。而一些中介机构的做法,加剧了制造企业的“用工荒”情况。
以笔者了解的两家制造企业为例。这两家企业均面临不同程度的用工短缺问题,其中一家A股上市企业2021年每隔3个月要更换一批临时工,另一家医疗器械企业近1/2的人员为临时工。据介绍,临时工工资为18元/小时,中介公司补贴7元/小时,实际到手工资为25元/小时,正式工到手工资则为18元/小时(正式工因需缴纳五险一金,缴纳前工资实际为31元/小时)。工人认为到手工资更可靠,因此导致绝大部分临时工不愿意长期留在工厂。这种思想传递到正式工群体中,又引发了一部分有经验的正式工离厂,从而形成恶性循环,即:临时工不仅没有缓解用工问题,反而成为影响正式工稳定性的不利因素。与此同时,一些中介机构为谋取利益,会采取一些方式让工作满3个月、技术娴熟的临时工离职,再更换一批临时工入厂。在留不住有经验的老员工、新员工生产效率和稳定性都较低的状况下,制造企业要缓解用工问题,必须主动进行变革。
一直以来,制造企业都在强调“精益生产”,以此提升效率、持续优化、创造价值。笔者以咨询服务过的制造企业为例,详细分析如何从短期缓解和长期发展两方面着手,帮助制造企业应对“用工荒”问题。
短期缓解:挖掘人效提升空间
大部分制造企业对工厂人员效率的分析指标以人均利润、人均收入等结果性指标为主,这些指标通常只能反映一段时间内人员的产出情况,或作同期、不同工厂间的人效产出对比,难以衡量生产工人实际生产过程的效率,也无法明确找出人员工作时间浪费、发现人员效率提升方向和具体提升点。因此,在人效分析中,还需要引入过程指标。
以某汽车零配件企业(下文简称X企业)为例。笔者团队根据该企业的生产特性,从设备综合效率(OEE)的计算原理中探索出了人员效率分析的创新方法。
考虑X企业工厂的人员配备与设备、机台的规划同频,工人生产时间与设备运转时间基本一致,因此将工人生产时间的统计维度分为A实际出勤时间、B计划负荷时间、C实际负荷时间、D实际产出时间、E价值时间。具体计算公式如下(见图1):
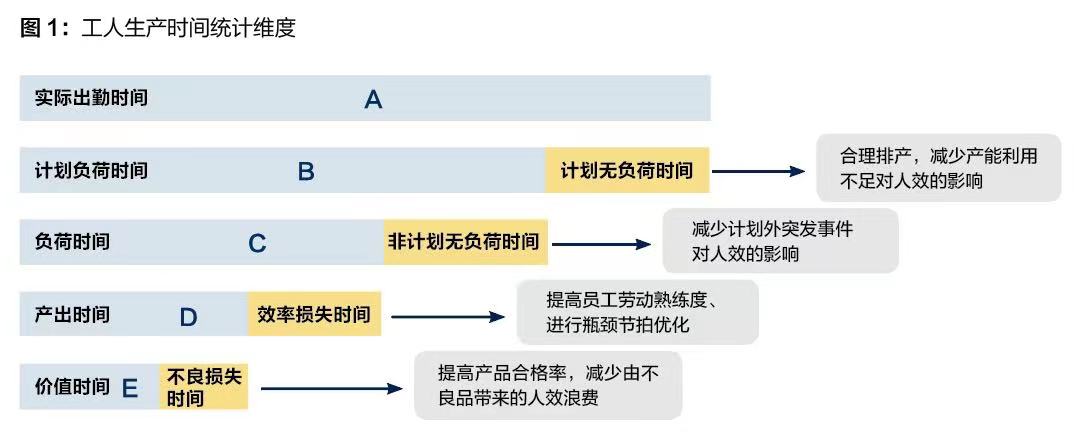
A实际出勤时间=工厂工人实际出勤打卡时间
B计划负荷时间=A实际出勤时间-计划无负荷时间
C负荷时间=B计划负荷时间-非计划无负荷时间
D产出时间=C负荷时间-效率损失时间
E价值时间=D产出时间-不良损失时间
通过分析工人的时间构成,可直接找出工人浪费的时间、工厂排产计划的不合理处、工人效率优化的方向等具体改善内容。同时,增加人员生产的过程性衡量指标,如:
有效工时利用率=E价值时间/A出勤时间
有效排产利用率=C负荷时间/A出勤时间
有效负荷产出=D产出时间/C负荷时间
有效负荷价值产出率=E价值时间/C负荷时间
计划负荷利用率=B计划负荷时间/A出勤时间
单位工时价值=工资总额/C负荷时间
对工厂人员效率进行具体分析,可形成人员效率分析的新思路:(1)横向比较各工厂关键人效指标、纵向比较各期数据,找出指标差异较大的工厂;(2)深入分析工厂各车间人效指标,找出指标差异较大的车间;(3)深入分析车间各产线和设备人效指标,找出指标差异较大的产线和设备;(4)指标层层分解,查找差异原因,提出解决思路,进行具体改善。如,a工厂有效负荷产出较低,便可深入了解a工厂的计划外突发事件,看哪些突发事件耗费的时间长、是否可减少处理时间、哪些突发事件未来可避免等;b工厂计划负荷利用率较低,可获取b工厂的排产计划(具体到产线、设备、机台、产品、产量等),找出其中的不合理处,压缩计划无负荷时间。
笔者在分析X企业下属一家工厂的人效时发现,工厂装配线3的有效负荷产出水平低于其他装配线。此装配线由6道工序组成,6道工序的节拍分别为:13秒、15秒、7秒、8秒、12秒和8秒,瓶颈工序为第2道工序,第3道工序和第4道工序的工人在做完本工序后都会等待几秒再进行生产。而通过分析各工序生产节拍可发现,工序3和工序4的总节拍为15秒,因此可将工序3和工序4合并,从而减少1名工人。
通过找出现有生产过程中的无效作业时间、优化排产计划、提升现有员工的效率,可减少工厂产线和机台的人员配备数量,及时有效缓解工人不足问题。
长期发展:加快智能制造进程
《中国制造2025》纲要中明确提出,把智能制造作为信息化和工业化深度融合的主攻方向。近期发布的《“十四五”智能制造发展规划》,更是对智能制造提出了诸多具体要求。
何为“智能制造”?在笔者看来,其是在多车间协同制造环境下,计划与执行一体化、物流配送敏捷化、质量管控协同化,实现混流生产与个性化产品制造,以及人、财、物、信息的集成管理(见图2)。“智能制造”能创造多大价值?以华为手机生产线为例,2014年之前,一条手机生产线需要配备86个工人,数字化转型后,从物料上线到手机包装完成的整个流程只需14个人;每28.5秒产出一部手机,生产效率为转型前的6倍。
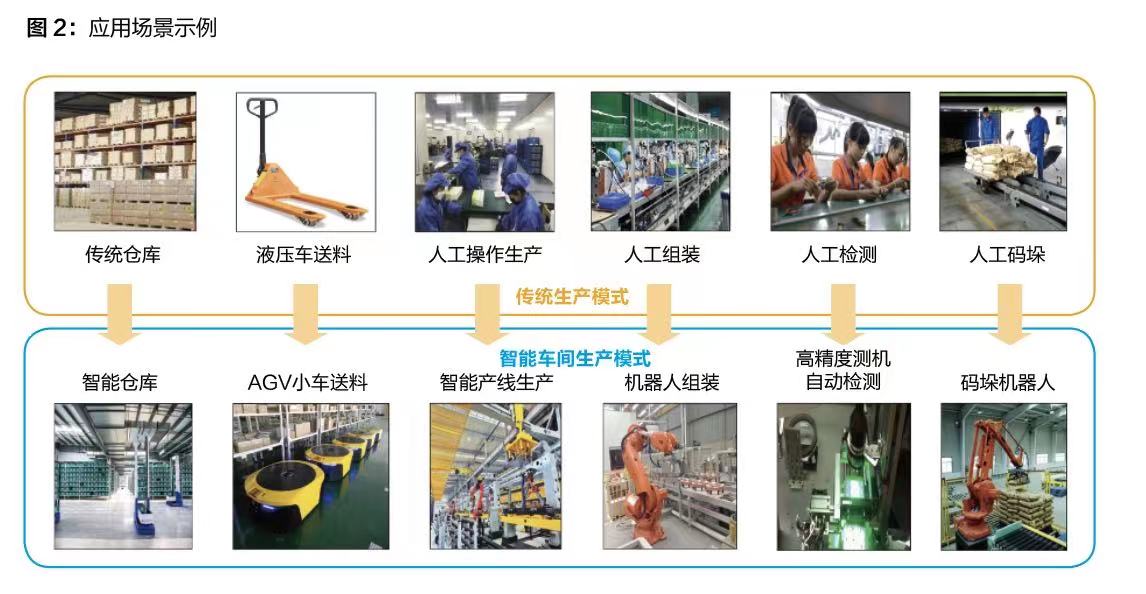
我国制造企业正处于数字化、智能化转型的过程之中,要更好地转向“智能制造”,首先应该认识到,“智能制造”非一朝一夕可完成,需要企业进行长期的信息系统规划与建设、持续的组织变革。总体而言,向智能制造的推行过程如下:
1.长期规划。开展工厂SWOT分析,明确工厂智能化车间建设目标和愿景,制定蓝图规划和实施路径。
2.全方位设计。包括以下六方面:
(1)工厂或车间布局设计:厂房设计、设备工艺能力分析与布置设计、物流方案设计等;
(2)设备、生产单元、生产线、车间自动化方案设计:加工、装配、检测、物流的自动化方案,以及关键设备的智能化提升方案;
(3)制造流程分析:工艺路线规划、工序设计、工序分配、产线平衡等分析;
(4)信息系统设计:支持车间规划、计划、运行管控、现场控制、数据采集、决策分析等的各类工业软件,如SCSDA、MES、APS等;
(5)支撑条件设计:包括车间物联网络、可视化显示与报警、信息安全与车间安全、数据总线与大数据存储、信息集成、人员规划等;
(6)业务流程梳理:包括计划流、执行流、物流、质量流、变更处置流、决策分析流等。
3.持续建设。包括以下六方面:
(1)虚拟仿真与验证:建立虚拟工厂(车间)模型,对生产及物流过程进行仿真分析,验证方案的可行性;
(2)车间自动化建设:根据制造工艺特点,建设加工、装配、检测、物流自动化生产系统,系统应具备足够的柔性,支持多品种混流生产;
(3)信息系统建设:包括现场控制类、生产管控类、工厂运营类、协同制造类等工业软件建设,目前企业多使用MES、ERP、CAPP、SCADA、SCM等系统;
(4)支撑环境建设:包括信息环境、管理环境(精益生产)、标准环境;
(5)系统集成和信息融合:智能工厂是一个复杂的系统平台,为避免信息孤岛,应实现系统集成和信息融合,这通常涉及产品生命周期端到端集成、横向集成和纵向集成;
(6)组织建设和人员培训:智能工厂建设必然要求组织结构调整和人员岗位变化。
4.模拟与运行。智能车间是信息空间和物理空间高度融合的场所,产品的加工、装配、检测和物流均在物理车间发生,而制造工艺的验证、生产计划的制定与优化、设备健康诊断与维护决策、质量缺陷识别和溯源分析、物流路径规划和调度等发生在信息空间中。
5.评价与优化。智能车间建设是一个不断迭代升级、演化的过程,在每一个建设周期结束后,都需要对实施效果进行评价,找出改善点,从而实现智能制造的不断迭代优化。
通过向智能制造转型,制造企业可真正实现“少人化、无人化”生产制造,从而更好地解决“用工荒”问题,同时,也能将人员从重复、低价值工作中解放出来,放在更可创造价值的岗位上。
毛婷,管理会计咨询顾问。联系方式:maoting3570@163.com。